CORRESTAT™ 5410
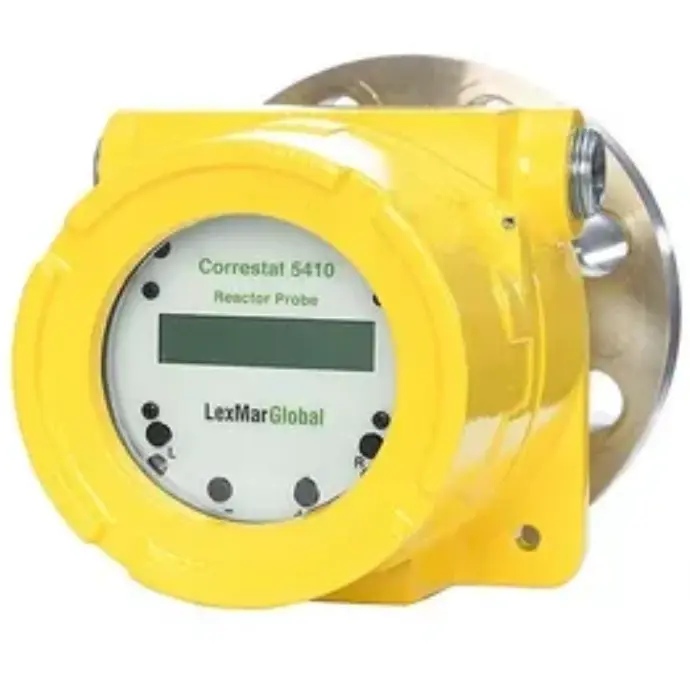
CORRESTAT™ 5410
Many process streams cannot be measured accurately with standard off-the-shelf electrostatic monitoring technology products. LexMar Global offers the unique Correstat™ 5410 electrostatic monitoring technology allowing for the measurement of two-phase mass flow in non-conductive media.
The Correstat™ 5410 electrostatic probe monitors conditions within gas phase reactors. The electrostatic monitor measures charge imbalances within the reactor chamber. With the electrostatic charge measurements provided by the Correstat™ 5410 in real-time, process stability can be improved and shutdowns avoided.
This electrostatic probe is installed directly into the reactor. It can be customized to fit into existing ports or nozzles with standard flanged connections. It is available in either an integral or remote probe and electronics configuration, to allow for a variety of process requirements.
BENEFITS
- Real-time indication of charge buildup in gas phase reactors
- Avoidance of reactor shutdowns caused by sheeting and agglomeration events
- Sensitivity ranges from pA to μA for optimum performance across varying conditions
- Feedback enables optimization of reactor conditions
- Simultaneous multi-parameter monitoring and DCS reporting via 4–20mA outputs
- Compact one-piece design (remote electronics version also available)
- Custom-designed probe for easy, low-cost installation into existing port
- No maintenance or spare parts required
- Enhanced safety, needs no nitrogen purging
- Real-time bipolar measurement
- User selectable output range and smoothing settings
The Correstat™ 5410 sensor is engineered to operate continuously 24 hours per day, seven days per week. It is designed for the harsh environment of fluidized bed reactors, requiring no maintenance or spare parts. Unlike traditional electrostatic probes, the Correstat sensor measures current. This keeps the potential of the active probe tip under 1 volt—compared to nearly 10 kV from traditional probes.
MECHANICAL
- Standard port (nozzle) sizes: 1.5" and 2" (others available)
- Flange mounting (300# typical)
- Cylindrical enclosure is 5.6" (14.3 cm) in diameter, 5.7" (19.4 cm) L
- All metals exposed to reactor are stainless steel
- Built to withstand significant impacts and reactor conditions
- Distance from flange face to tip of sensor is customizable
- Pressure tested up to at least 1000 psi (higher pressure systems available)
ENVIRONMENTAL
- ATEX/IECEx (Ex II 2 G/Ex db ia IIC T3 Gb)
- cULus Listed for Class I, Division 2, Groups A, B, C, and D
- Operating Temperature Range: -20°C up to 55°C
- Consult LexMar Global for high temperature applications
ELECTRICAL
- Two ¾" NPT entries for power and analog output signal
- 20 or 230 VAC 50/60 Hz or 24 VDC, 10 VA
- Intrinsically safe probe connection
- Probe tip operates at <1 volt, eliminating the dangers of a high voltage source within the reactor
- 4–20mA bipolar outputs, two user-selected parameters can be assigned as outputs
- Full scale output range selectable from ±0.1 nA to ±1000 nA of electrostatic current
- User selectable signal damping
- ATEX/IECEx (Ex II 2 G/Ex db ia IIC T3 Gb)
- cULus Listed for Class I, Division 2, Groups A, B, C, and D
- Operating Temperature Range: -20°C up to 55°C
- Consult LexMar Global for high temperature applications